Research Area

Dirty Energy, Smart Technology
Dirty energy smart technology is widely investigated recently, which is converting dirty energy (biomass, coal and tar etc.) to renewable energy by using chemical reaction processes. It is very important to find the way using fossil fuel smartly due to the current sharp increasing trends of oil prices. As one of dirty energy smart technology, KAIST has been studying diesel reforming technology for a solid oxide fuel cell (SOFC) system in 10 years.

Diesel Reforming
Much efforts has been made to feed diesel to the SOFC system because diesel has well constructed infrastructure and high H2 storage density. However, carbon deposition on the reactor was found to be the main barrier from KAIST research and we found that ethylene has critical role in carbon deposition process. We also found the ethylene suppression and cleaning methods and the research has been successful through fuel injector and post-reformer research.

Diesel reforming catalysts are deactivated rapidly during operation because of coke formation, sulfur poisoning and catalysts sintering. Especially, coke formation is severe in diesel reforming because of its high contents of high hydrocarbons. Therefore, inhibition of catalyst deactivations is required to increase reforming efficiency. For this reason, we are researching from reforming catalysts to integrated kW reformer.
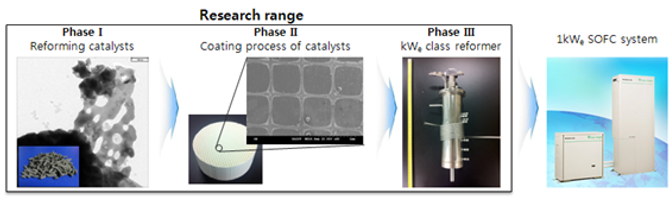